Gemelli digitali per l'industria meccanica
Cos'è un gemello digitale, cosa può fare e quali requisiti deve soddisfare per essere pratico nell'industria meccanica? I ricercatori del Fare all'ETH e tre aziende hanno indagato su questa domanda e hanno ottenuto risultati sorprendenti.
- Leggi
- Numero di commenti
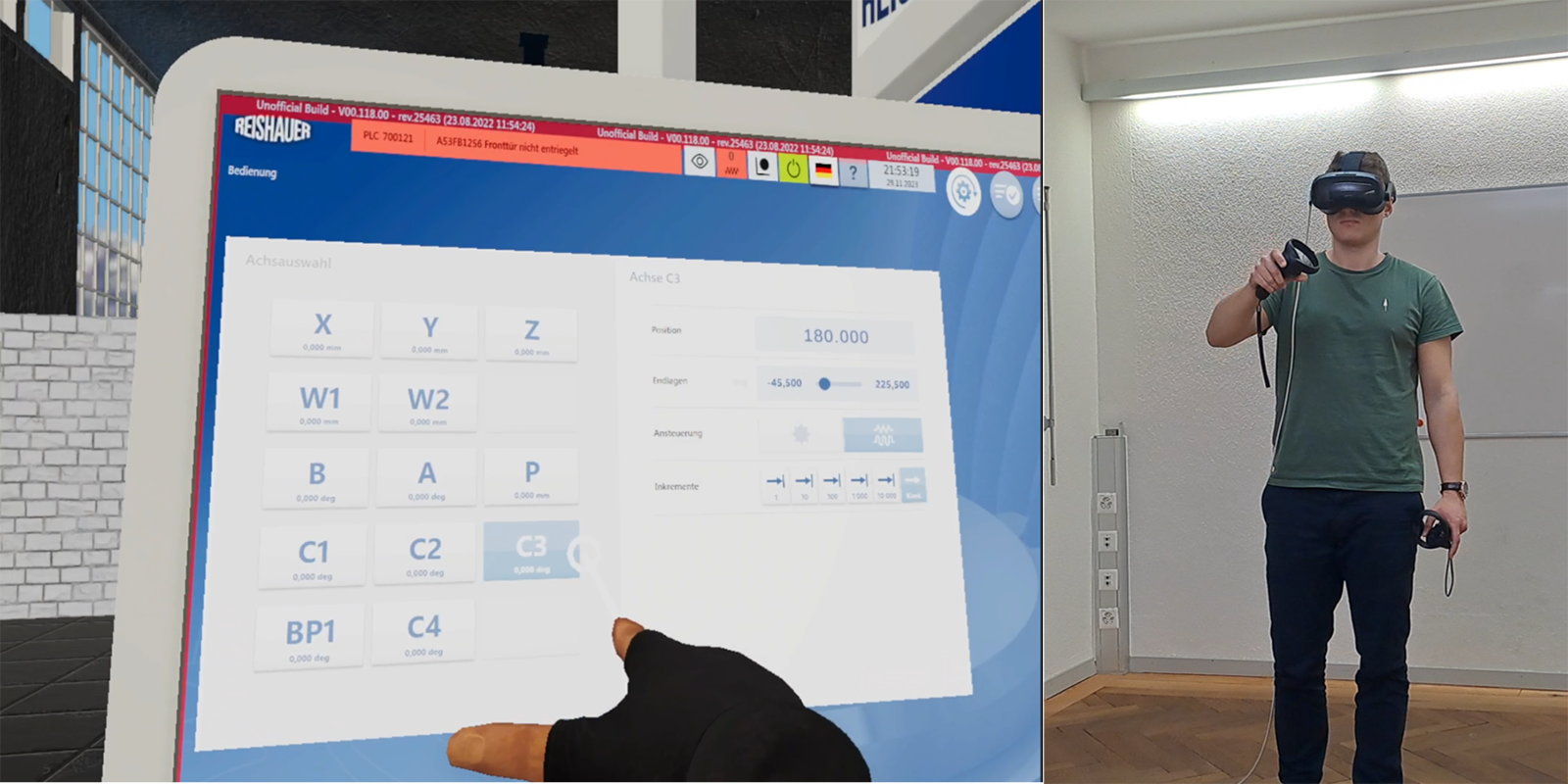
Joy Gisler (ETH di Zurigo), Florian H?nni (Reishauer AG) e Alexander Farger (Siemens) ci hanno illustrato il progetto.
Le repliche digitali di macchine reali che possono essere utilizzate virtualmente sono chiamate gemelli digitali. "L'ETH sta lavorando molto all'ETH per la ricerca sulla realtà virtuale e sui gemelli digitali", afferma Joy Gisler, ricercatore dell'Istituto per le macchine utensili e la produzione. "A un certo punto, si vuole sapere a cosa serviranno gli sviluppi nella pratica". La questione ha suscitato grande interesse anche da parte dell'industria e ha portato a un progetto finanziato da Innosuisse intitolato "Virtual Reality Extension for Digital Twins of Machine Tools", che ha studiato due applicazioni specifiche:
- Come deve essere strutturato un corso di formazione su una macchina virtuale (gemello digitale) affinché quanto appreso possa essere implementato sulla macchina reale?
- ? possibile calcolare e simulare in modo affidabile l'analisi delle collisioni di un processo di rettifica su una rettificatrice virtuale (gemella digitale)?
"L'ETH sta lavorando molto all'attività di ricerca sulla realtà virtuale e sui gemelli digitali. A un certo punto, si vuole sapere a cosa servono gli sviluppi nella pratica".Joy Gisler, ETH di Zurigo
Imparare in digitale è altrettanto valido che sulla macchina reale
Per utilizzare le complesse macchine del produttore di rettificatrici Reishauer è necessaria una formazione approfondita. In un test, 20 persone sono state addestrate direttamente sulla macchina fisica o digitalmente, utilizzando un gemello digitale in realtà virtuale.
Con il metodo fisico, durante la formazione la macchina non è decisa per la produzione. Tre operatori sono stati addestrati contemporaneamente da un istruttore sulla macchina, il che ha richiesto 2,5 ore.
Il metodo digitale, invece, poteva essere eseguito da tutti gli operatori indipendentemente dalla macchina reale, in qualsiasi momento e luogo. Gli operatori hanno avuto bisogno di soli 50 minuti per farlo. L'interazione con il gemello digitale è avvenuta in modo intuitivo, utilizzando i movimenti della mano e del punto registrati dai sensori Sensoryx.
Una settimana dopo l'addestramento digitale o fisico, è stato effettuato il test sulla macchina reale. ? emerso che i compiti sono stati risolti ugualmente bene da entrambi i gruppi. La conclusione è che la formazione digitale ha un vantaggio: è più veloce, può essere svolta indipendentemente dal tempo e dal luogo e la macchina reale può produrre senza interruzioni.
Le collisioni potenziali possono essere facilmente simulate
Le rettificatrici per ingranaggi devono lavorare con una precisione micrometrica, il che richiede una guida precisa del pezzo. Per evitare che il pezzo da rettificare entri in collisione con la macchina durante il processo di rettifica, vengono sviluppati complessi algoritmi per escludere le collisioni. La seconda indagine era volta a determinare se i gemelli digitali potessero essere utilizzati per calcolare tali analisi di collisione in modo più rapido, semplice e con meno sforzo. Anche in questo caso, i risultati sono estremamente soddisfacenti: è stata raggiunta la precisione richiesta nel rilevamento delle collisioni e l'analisi viene eseguita con la semplice pressione di un pulsante, risparmiando tempo.

Sfida tecnologica
Quello che ora sembra così semplice era una grande sfida tecnologica: si doveva creare un unico gemello digitale a partire dai tre singoli componenti di macchina, sistema di controllo e algoritmo. In altre parole, si doveva costruire una versione digitale della macchina Reishauer, dotata del sistema di controllo Siemens e del complesso algoritmo.
"Vediamo un grande potenziale nell'uso dei gemelli digitali nella formazione del personale operativo e di manutenzione. Il collegamento con la realtà virtuale porta l'insegnamento dei contenuti formativi a un livello superiore".Alexander Farger, Siemens Svizzera AG
Tutti ne hanno beneficiato
Per realizzare questo progetto sono stati necessari tutti i partner coinvolti. I ricercatori del Fare all'ETH, guidati dal professore Andreas Kunz, sono riusciti a sviluppare e ad applicare nella pratica la loro ricerca. Alexander Farger di Siemens conclude: "I produttori e gli operatori di macchine stanno già utilizzando con successo i nostri prodotti "Create and Run myVirtual Machine" per creare gemelli digitali e ottimizzare i processi produttivi. Tuttavia, vediamo anche un grande potenziale nell'uso dei gemelli digitali nella formazione del personale operativo e di manutenzione. Il collegamento con la realtà virtuale porta l'insegnamento dei contenuti formativi a un livello superiore. La soluzione è interessante anche per i centri di formazione, in quanto offre un modo semplice per imparare a utilizzare macchine con tecnologie e livelli di complessità diversi.
"Grazie al supporto di Innosuisse, abbiamo potuto valutare due opzioni per il controllo delle collisioni. Entrambe hanno funzionato".Florian H?nni, Reishauer AG
Florian H?nni di Reishauer vede diversi vantaggi in questo progetto: "Grazie al supporto di Innosuisse, abbiamo potuto valutare due opzioni per i test di collisione. Entrambe hanno funzionato. Integreremo il controllo delle collisioni nel nostro software di progettazione, ma utilizzeremo un approccio tecnologico diverso. Sia per H?nni che per Farger, i progetti con l'ETH di Zurigo sono di grande valore perché sanno fin dall'inizio di avere accesso agli specialisti assoluti del settore e la comunicazione è sempre aperta e paritaria.
Contatto:
Istituto per le macchine utensili e la produzione,Professore Andreas Kunz
Siete interessati ad altre emozionanti storie di "Notizie per l'industria"?
Iscriviti alla nostra newsletter
lato esternoSeguici su LinkedIn
Siete alla ricerca di partner di ricerca presso l'ETH di Zurigo?
Contattateci Relazioni industriali dell'ETH