David rétréci à la taille d'un millimètre
Des chercheurs zurichois ont imprimé le David de Michel-Ange en miniature métallique. Ils démontrent ainsi le potentiel d'un procédé d'impression 3D spécial développé à l'ETH.
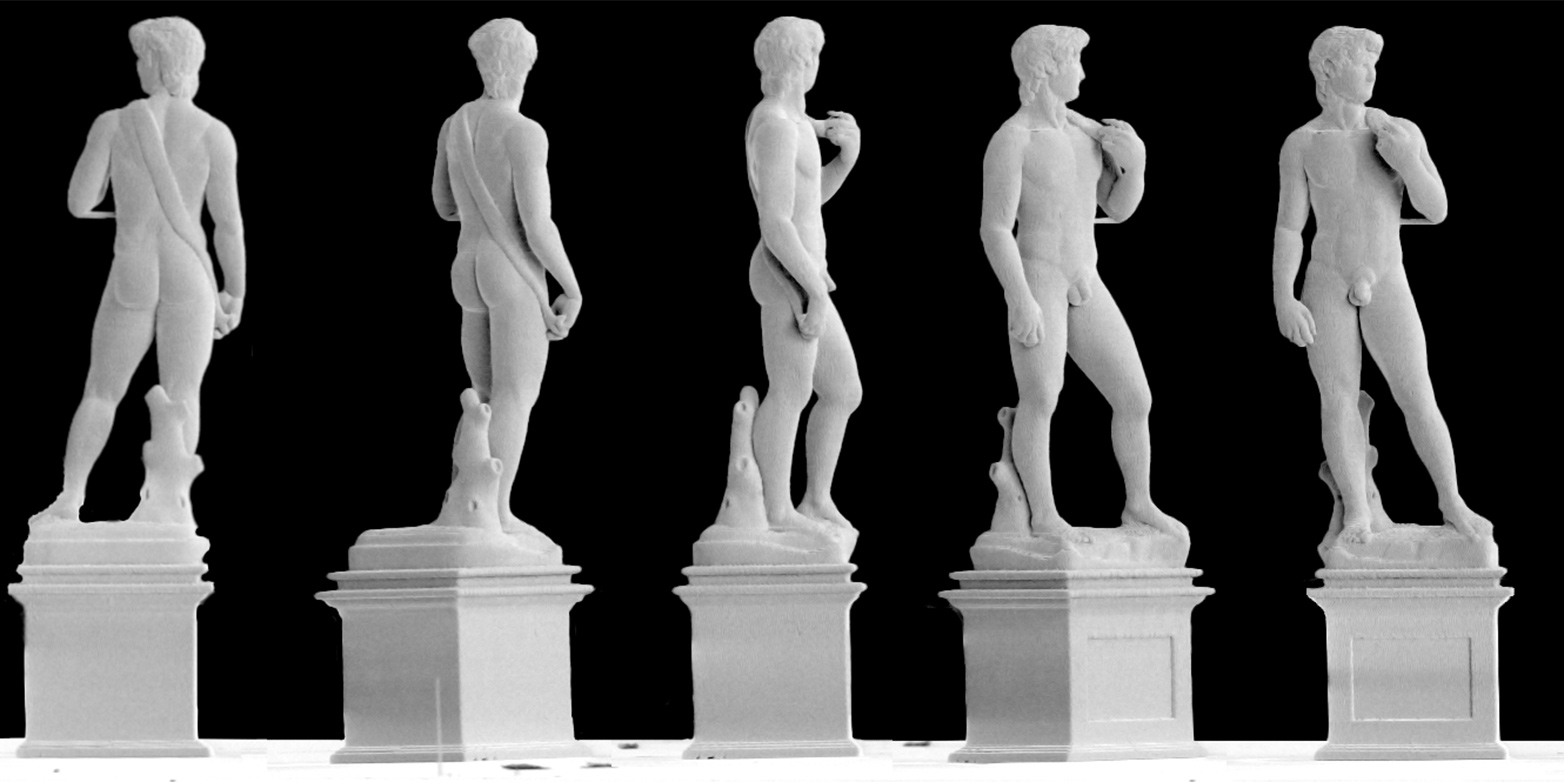
Il est là, sur son socle : le David de Michel-Ange. Cette sculpture est célèbre dans le monde entier, presque tous les enfants la connaissent. Pourtant, ce David ne mesure qu'un millimètre avec son socle et n'est pas en marbre comme l'original de plus de cinq mètres, mais en cuivre pur.
La miniature a été créée par impression 3D par Giorgio Ercolano de la société Exaddon, une émanation du spin-off de l'ETH Cytosurge, en collaboration avec l'équipe du professeur de l'ETH Tomaso Zambelli du laboratoire de biocapteurs et de bioélectronique. Zambelli et son équipe ont développé le procédé d'impression 3D utilisé il y a quelques années. Il est ainsi possible de fabriquer des structures métalliques à l'échelle nanométrique et micrométrique.
L'élément central du procédé est une micropipette couplée à un ressort à lame (cantilever), la force avec laquelle la pointe de la pipette touche le substrat étant observée. Les chercheurs peuvent ainsi déposer par voie électrochimique et avec une grande précision des métaux en solution sur une plaque de base conductrice. Couche après couche, ils peuvent ainsi construire de minuscules structures métalliques en une seule opération, de manière automatisée gr?ce à la mesure optique de la force. La société Exaddon a repris le procédé d'impression de micrométaux et l'a amélioré, notamment en l'accélérant.
Des géométries compliquées imprimables
Pour démontrer le potentiel de la technologie, Ercolano a imprimé le micro-David. Jusqu'à présent, ils avaient surtout imprimé de minuscules colonnes ou spirales. "Mais le procédé permet d'imprimer n'importe quelle structure ou géométrie complexe", explique Ercolano. La sculpture a été imprimée en un seul passage, sans structure de support ni gabarit. Les chercheurs n'ont pas non plus eu besoin de cuire ou de durcir la figurine après sa fabrication. Ercolano et ses collègues viennent de présenter leurs résultats dans la revue spécialisée Micromachines.
Les données de la sculpture de David qui commandent l'imprimante sont librement disponibles sur Internet. "J'aurais même pu imprimer la salle dans laquelle la statue est exposée, car le jeu de données comprend également cette salle", sourit Ercolano. Pour produire David sans salle d'exposition, il a donc d? nettoyer le jeu de données.
La résolution fixe une limite inférieure
Ercolano a imprimé David en deux tailles : en premier lieu, une sculpture d'un millimètre et une autre dix fois plus petite. "La figure la plus petite n'est pas plus haute que le socle de la plus grande", explique le chercheur. La résolution atteint toutefois ses limites avec des structures aussi petites. L'impression de micro-objets métalliques commence à un micromètre. La plage principale pour l'impression de micro-objets plus complexes et détaillés se situe entre 100 micromètres et un millimètre. Il y a également un monde entre le modèle d'un millimètre et celui dix fois plus petit en termes de temps : pour produire le "grand" David, l'appareil a eu besoin de 30 heures, contre 20 minutes pour la plus petite édition.
En théorie, ce système d'impression permet de fabriquer des objets d'une taille allant jusqu'à cinq millimètres. Toutefois, la cartouche d'impression ne contient qu'un microlitre d'"encre", ce qui suffit tout juste pour la fabrication du plus grand David. Avec un seul remplissage, il est toutefois possible d'imprimer des centaines, voire des milliers d'objets minuscules, ce qui correspond à la puissance du procédé d'impression.
Un principe qui fonctionne
Tomaso Zambelli est lui aussi très satisfait du résultat. "Nous sommes heureux qu'une technologie issue de notre laboratoire de recherche ait trouvé le chemin de la pratique", déclare le professeur de l'ETH. "Le fait qu'un groupe indépendant ait pu reprendre notre procédé d'impression 3D et même l'améliorer montre qu'il fonctionne vraiment", ajoute-t-il.
C'est en premier lieu le secteur de l'électronique qui s'intéresse à ce procédé d'impression. Cette méthode permet par exemple de relier entre elles des puces informatiques ou de réparer avec précision des composants microélectroniques. Bien que d'autres métaux puissent être imprimés, comme le platine, l'or, le nickel ou l'argent, les clients sont les plus demandeurs de cuivre. "Neuf demandes sur dix concernent le cuivre", explique Ercolano.
Ce projet a été soutenu par Innosuisse, l'agence suisse pour la promotion de l'innovation.
Référence bibliographique
Ercolano G, van Nisselroy C, Merle T, V?r?s J, Momotenko D, Koelmans WW, Zambelli T. Additive manufacturing of sub-micron to sub-mm metal structures with hollow AFM cantilevers. site externeMicromachines 2020, 11(1), 6 ; site externehttps://doi.org/10.3390/mi11010006 (registering DOI), open access - 18 déc. 2019.