Armature de sel imprimée en 3D pour un implant osseux
Des chercheurs de l'ETH produisent du magnésium à porosité structurée à l'aide d'une armature de sel imprimée en 3D, qui convient pour des implants osseux biodégradables.
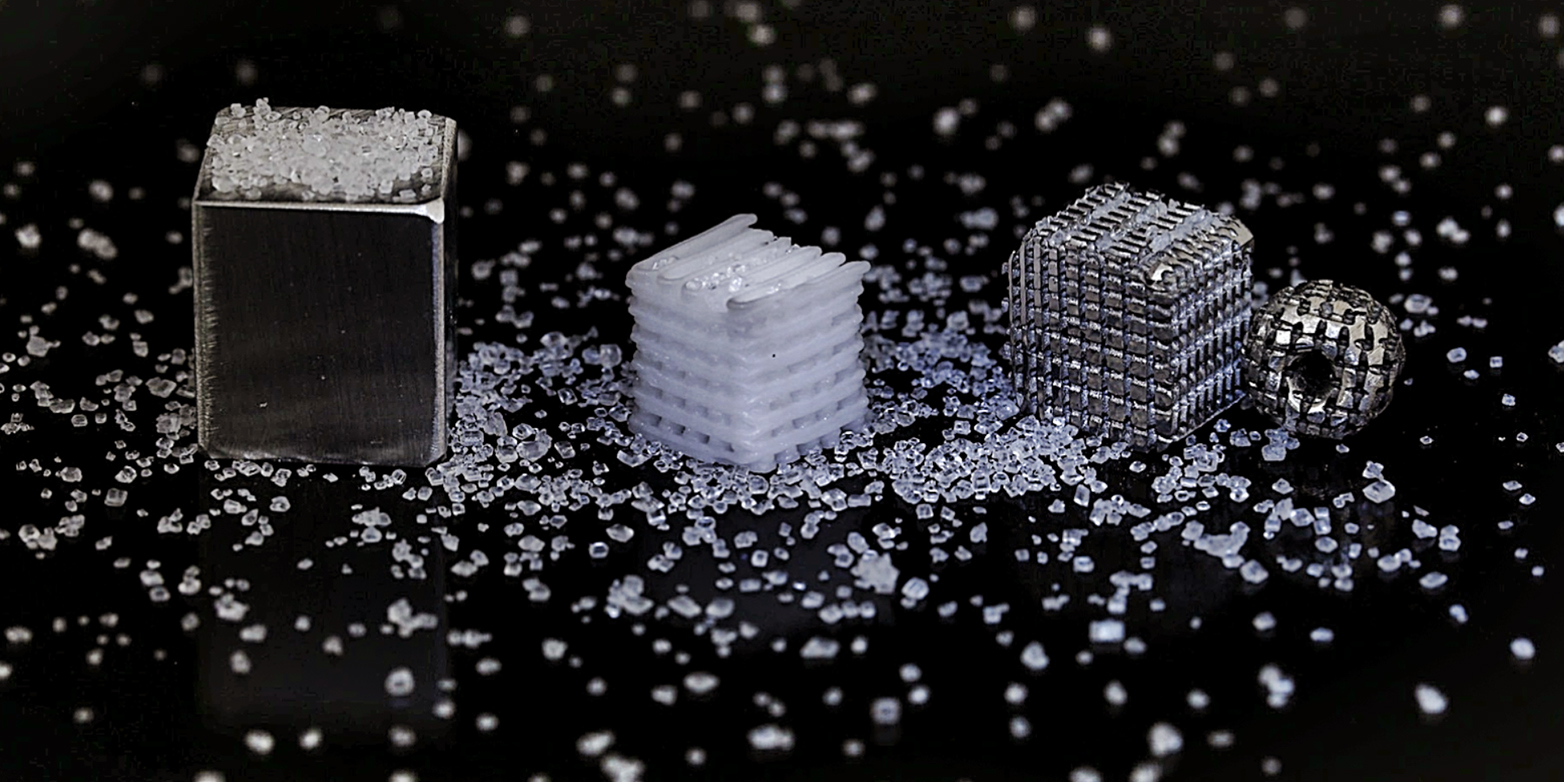
En cas de fractures osseuses compliquées ou même de parties osseuses manquantes, les chirurgiens utilisent généralement des implants métalliques. Outre le titane, qui n'interagit ni chimiquement ni biologiquement avec les tissus, le magnésium et ses alliages sont des matériaux de choix. Les implants en ce métal léger ont l'avantage d'être dégradés par le corps et d'absorber le magnésium sous forme de substance minérale. Ainsi, aucune autre opération n'est nécessaire pour retirer l'implant. Pour une guérison rapide, l'implant ou ses surfaces doivent être con?us de manière à ce que les cellules productrices d'os puissent facilement s'y implanter, voire s'y développer.
Des chercheurs en matériaux de l'ETH Zurich ont donc mis au point un nouveau procédé pour fabriquer des implants en magnésium qui disposent de nombreux pores disposés de manière régulière et qui sont malgré tout stables. Leur développement sera prochainement publié dans la revue spécialisée page externeMatériaux avancés publiés .
Magnésium à porosité structurée
Pour obtenir une structure de base poreuse, les chercheurs ont d'abord imprimé une structure tridimensionnelle en treillis de sel à l'aide d'une imprimante 3D. Comme le sel de cuisine pur et conventionnel n'a pas les propriétés nécessaires pour être imprimé, les chercheurs ont développé à cet effet une p?te de sel sous forme de gel. Le diamètre des barres de la grille et leur espacement peuvent être réglés selon les besoins lors de l'impression. Pour consolider la structure saline, elle a ensuite été frittée. Lors du frittage, les matériaux à grain fin sont fortement chauffés. Les températures sont toutefois inférieures au point de fusion de la matière afin de préserver la structure de la pièce.
Dans une étape suivante, les chercheurs en matériaux ont infiltré l'espace poreux entre les barres de sel avec du magnésium fondu. "Cette ébauche est mécaniquement très stable et peut être facilement usinée par polissage, tournage et fraisage", explique J?rg L?ffler, professeur de physique et de technologie des métaux au Département de science et ingénierie des matériaux. Après le traitement mécanique, les chercheurs ont détaché le sel et ont ainsi obtenu l'implant en magnésium pur avec de nombreux pores disposés de manière régulière.
Décisif pour le succès clinique
"La possibilité de contr?ler la taille des pores ainsi que leur répartition et leur direction dans le matériau est décisive pour le succès clinique de l'implant, car les cellules ostéogènes aiment se développer dans de tels pores", souligne le professeur de l'ETH. Et c'est précisément ce qui importe pour qu'un implant s'intègre rapidement à l'os.
Outre l'infiltration avec du magnésium, le procédé nouvellement développé pour la fabrication de telles structures auxiliaires à partir de sel laisse une grande marge de man?uvre pour d'autres matériaux. Les co-auteurs Martina Cihova et Kunal Masania partent du principe qu'il est possible de cette manière de doter également des polymères, des céramiques ou d'autres métaux légers d'une géométrie de pores contr?lée.
L'idée de ce nouveau procédé de fabrication est née dans le cadre du travail de master de la première auteure, Nicole Kleger. Son travail a été encouragé par une bourse d'excellence et d'opportunité de l'ETH Zurich. Celle-ci a en outre été récompensée par une médaille de l'ETH pour des travaux de master exceptionnels. Entre-temps, Kleger travaille comme doctorante dans le groupe des matériaux complexes du professeur de l'ETH André Studart, sous la direction duquel l'échafaudage de sel a été imprimé en 3D. Dans le cadre de sa thèse de doctorat, la chercheuse s'emploie désormais à développer le procédé d'impression 3D.
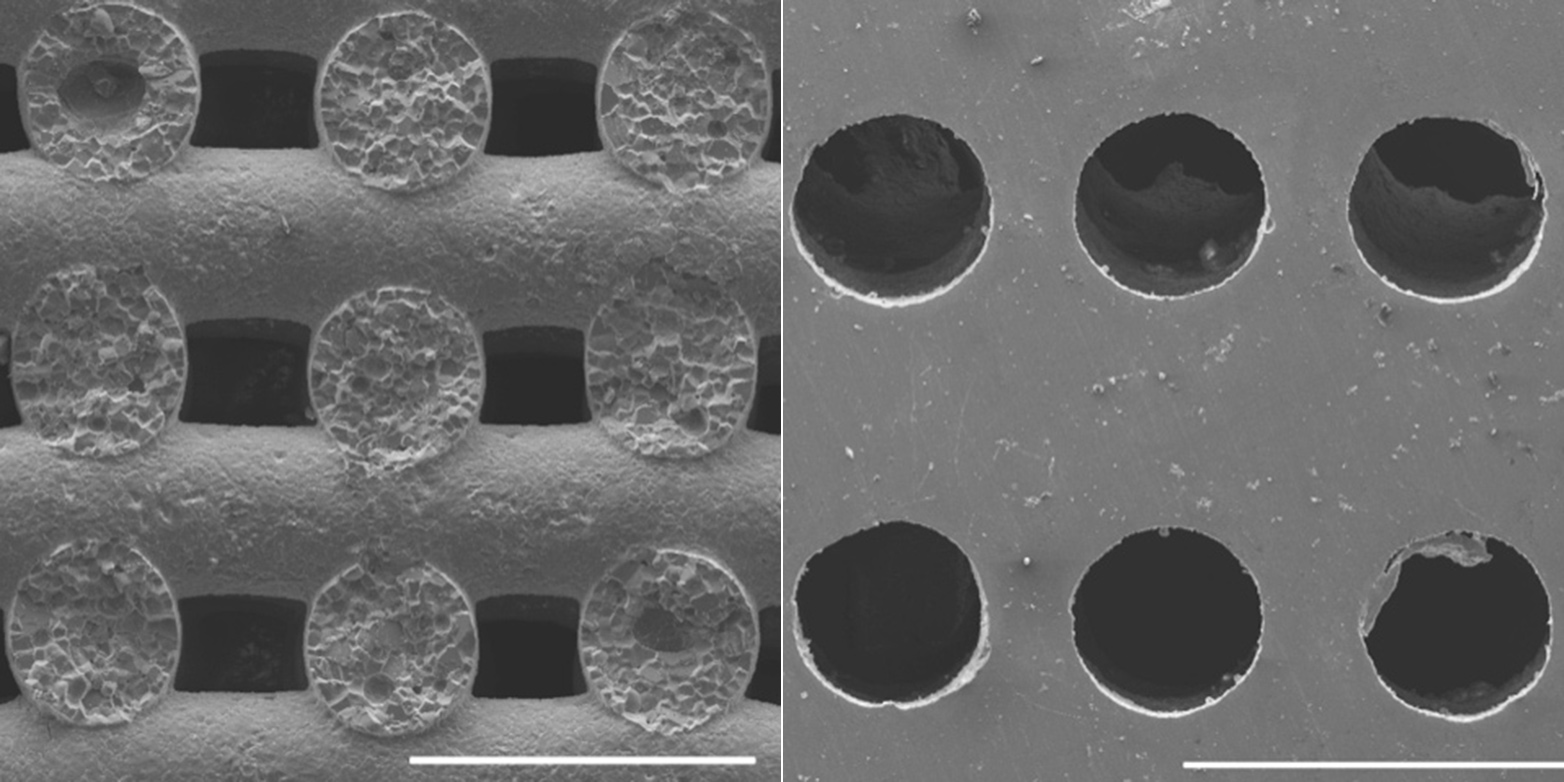
Référence bibliographique
Kleger N, Cihova M, Masania K, Studart AR, L?ffler JF. Impression 3D de sel comme modèle pour le magnésium à porosité structurée. Adv. Mater. 2019, 1903783, page externedoi : 10.1002/adma.201903783