Impression 3D de micro-objets métalliques
L'impression 3D est un outil de plus en plus important dans la fabrication. Des chercheurs de l'ETH viennent de mettre au point un nouveau procédé d'impression 3D qui permet de fabriquer des objets à l'échelle du micromètre à partir de plusieurs métaux et avec une haute résolution spatiale.
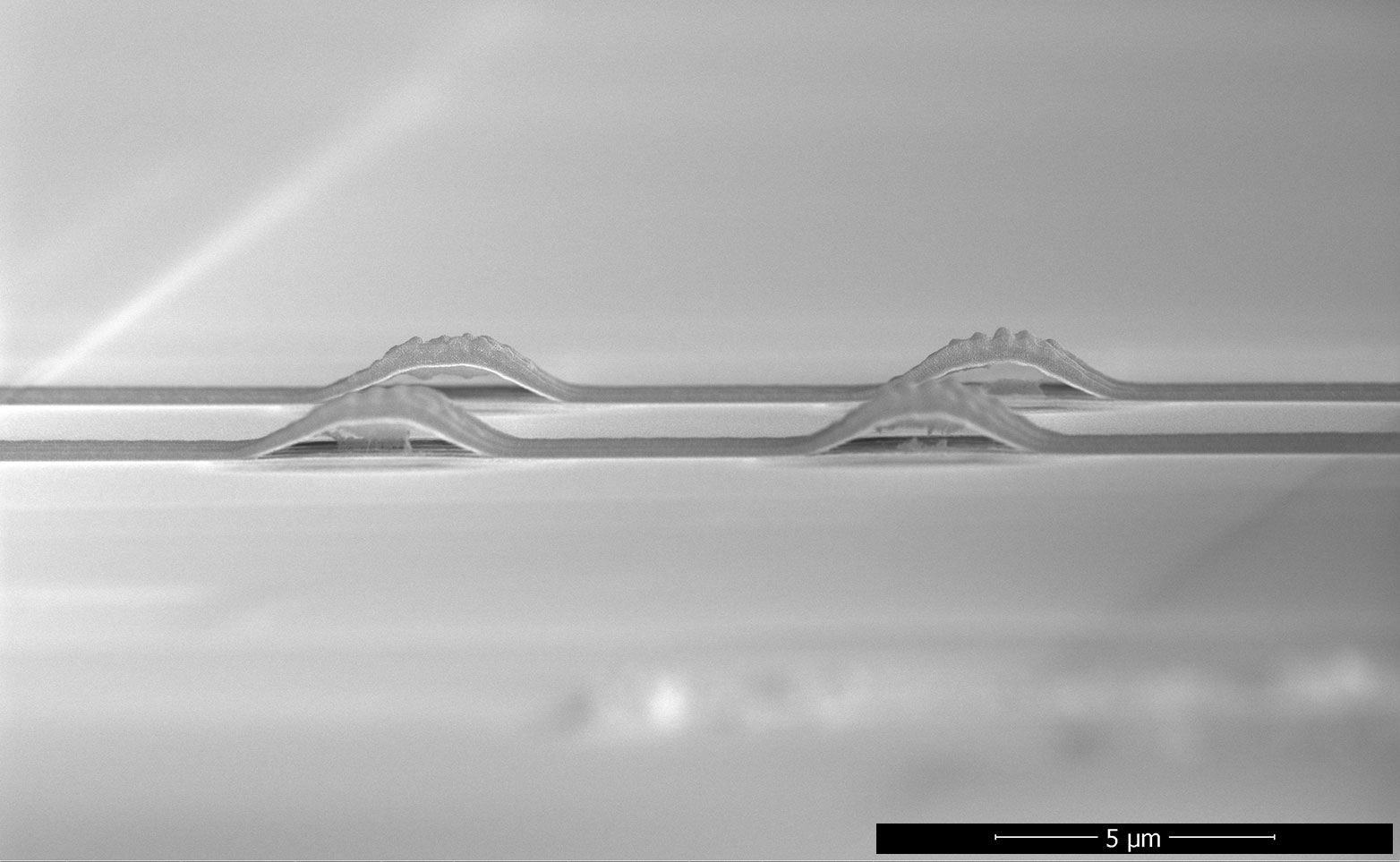
Aujourd'hui, les imprimantes 3D peuvent imprimer presque tout, des prototypes en cours de fabrication aux organes artificiels et aux maisons complètes. Dans le domaine microscopique en particulier, la fabrication additive, comme on appelle aussi l'impression 3D, rend possible la fabrication de structures qui ne pourraient pas être réalisées avec d'autres procédés comme la lithographie. Jusqu'à présent, les structures métalliques à l'échelle du micromètre constituaient toutefois un point faible de la fabrication additive.
Des chercheurs de l'ETH Zurich autour de Ralph Spolenak, professeur au laboratoire de nanométallurgie du Département de science des matériaux, ont maintenant développé, en collaboration avec Dimos Poulikakos du Département de chimie et des sciences biologiques appliquées et Renato Zenobi du Département de chimie et des sciences biologiques appliquées, un procédé qui permet même d'imprimer simultanément deux métaux avec une résolution spatiale de 250 nanomètres.
Des alternatives à l'encre
Les méthodes traditionnelles d'impression 3D métallique sont basées sur l'encre, c'est-à-dire que le métal souhaité est déposé sur une surface sous forme de nanoparticules en suspension à travers une buse d'impression. L'un des aspects positifs de ces encres est qu'elles peuvent être produites avec une grande variété de matériaux, mais il existe aussi des inconvénients de poids. "De tels procédés nécessitent un post-traitement par chauffage du résultat de l'impression, ce qui entra?ne un rétrécissement et une porosité prononcée dans le matériau", explique Alain Reiser, doctorant dans le groupe de travail de Spolenak et premier auteur de l'étude publiée aujourd'hui dans page externeNature Communications étude publiée. "Cela signifie généralement que les structures métalliques sont moins conductrices, moins stables mécaniquement et, en outre, souvent contaminées par des composés organiques du solvant".
Imprimer avec des ions
Pour résoudre ce problème, les scientifiques de l'ETH ont choisi la voie directe : le métal n'est désormais plus déposé sous forme de nanoparticules, mais transporté sous forme d'ions métalliques chargés électriquement. Ceux-ci sont obtenus dans la buse sous pression en appliquant une tension électrique à partir d'une "anode sacrificielle" constituée du métal correspondant. Les ions sont ensuite pulvérisés dans un solvant par des forces électriques sur la surface à imprimer, où ils perdent leur charge et se recomposent en métal.
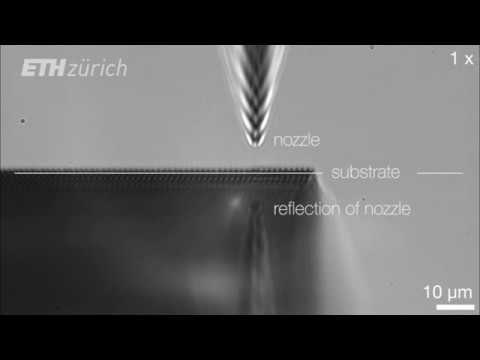
Les métaux ainsi imprimés sont denses et présentent des propriétés électriques et mécaniques équivalentes à celles des films minces fabriqués de manière traditionnelle. Dans ce contexte, le nouveau procédé d'impression offre une résolution de 250 nanomètres à une vitesse d'impression de dix voxels par seconde (un voxel est un élément de volume, similaire au pixel dans l'impression 2D). Ce procédé est donc dix fois plus rapide que les procédés d'impression électrochimiques existants.
Des métaux en alternance
Le nouveau "procédé d'impression redox électro-hydrodynamique" présente encore un autre avantage décisif, comme le souligne Reiser : "En imprimant directement au moyen d'ions métalliques, sans passer par une encre, nous pouvons même imprimer deux métaux simultanément ou en alternance. Cela nous permet de fabriquer des structures métalliques aux propriétés chimiques, électriques ou mécaniques contr?lables localement". Pour y parvenir, les chercheurs utilisent une double buse d'impression dans laquelle se trouvent deux anodes sacrificielles différentes. Il est désormais possible de contr?ler quel métal doit être imprimé, quand, où et à quelle concentration, simplement en appliquant des tensions.
L'utilisation d'une seule buse de pression facilite également le positionnement précis des deux métaux. Il est possible de passer d'un métal à l'autre jusqu'à dix fois par seconde. De cette manière, Spolenak et ses collaborateurs ont par exemple réussi à imprimer des colonnes de seulement 250 nanomètres de large contenant des sections de cuivre et d'argent en alternance. En ajustant l'alliage des deux métaux, ils ont pu contr?ler avec précision la porosité locale et donc la rigidité et la résistance des nano-colonnes.
Des applications variées
Les applications possibles de cette nouvelle technique sont nombreuses. Les scientifiques de l'ETH travaillent actuellement avec des experts en électronique imprimée à la fabrication de fils de connexion très fins pour des semi-conducteurs organiques par impression 3D. A l'avenir, ils souhaitent également élargir la palette des métaux utilisés (jusqu'à présent, le cuivre, l'argent et l'or ont été testés), par exemple avec des matériaux magnétiques. Selon Alain Reiser, l'objectif à long terme devrait être la fabrication de photodétecteurs, de circuits intégrés imprimés et de métamatériaux mécaniques.
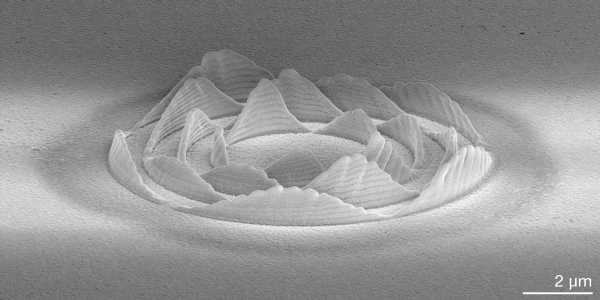
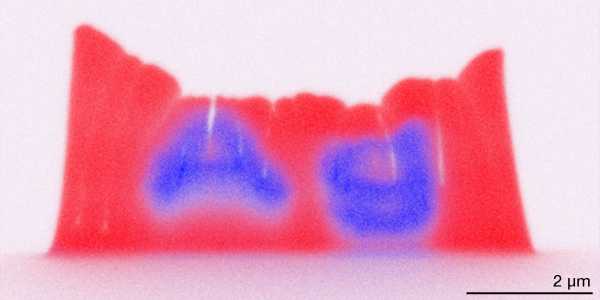
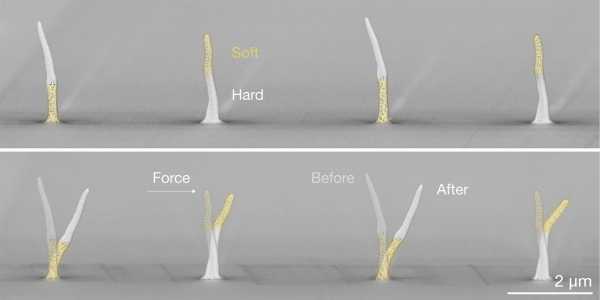
Référence bibliographique
Reiser A et.al : Multi-metal electrohydrodynamic redox printing 3D at the submicron scale. Nature Communications 10, 1853 (2019). DOI : page externe10.1038/s41467-019-09827-1