Architecture des miroirs
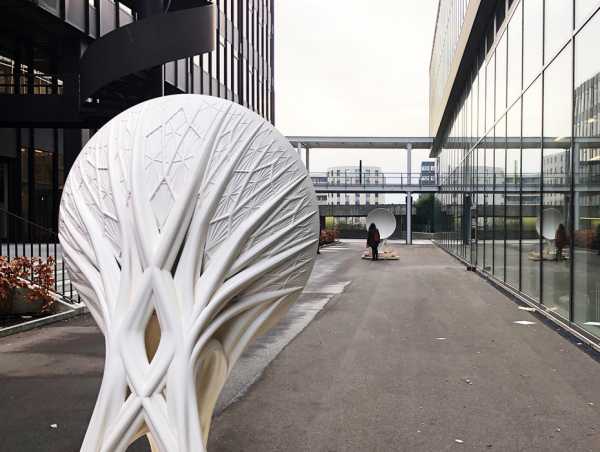

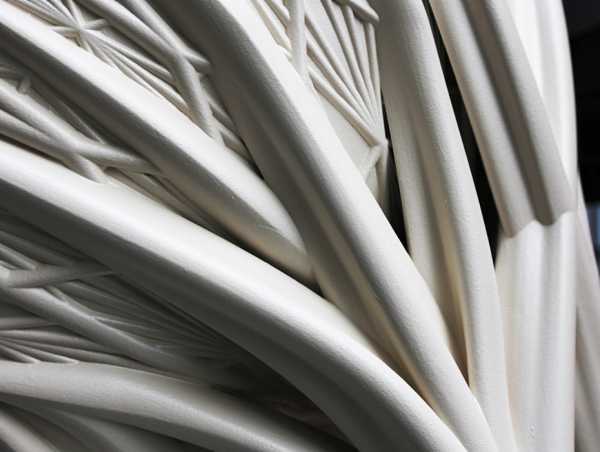
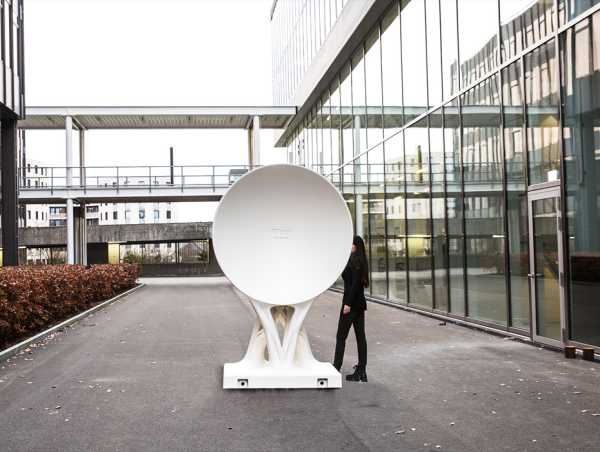
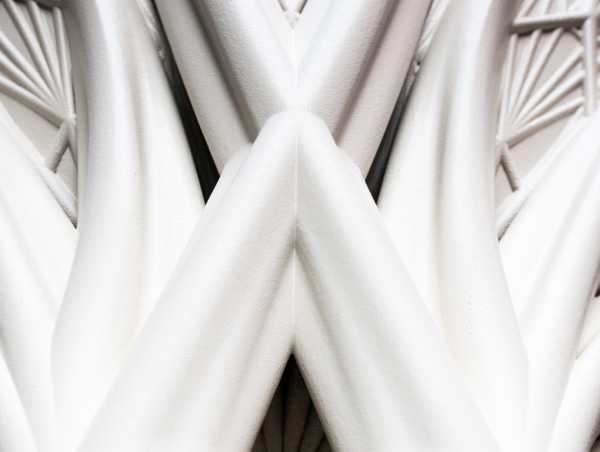
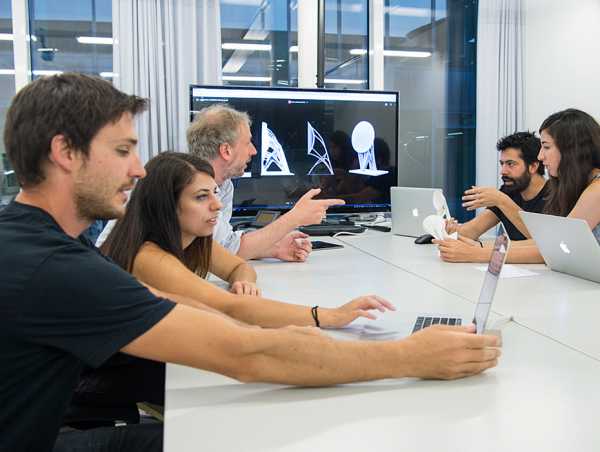
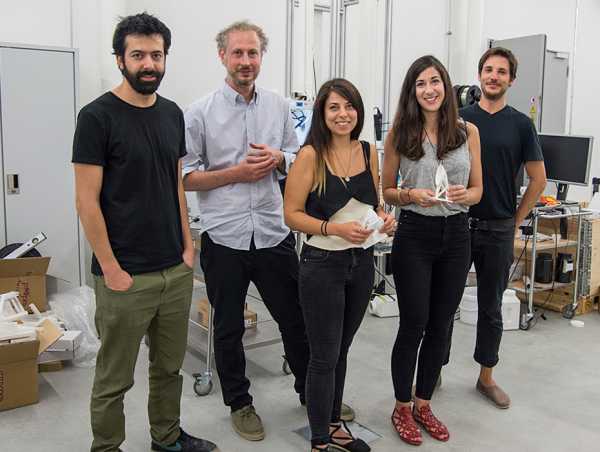
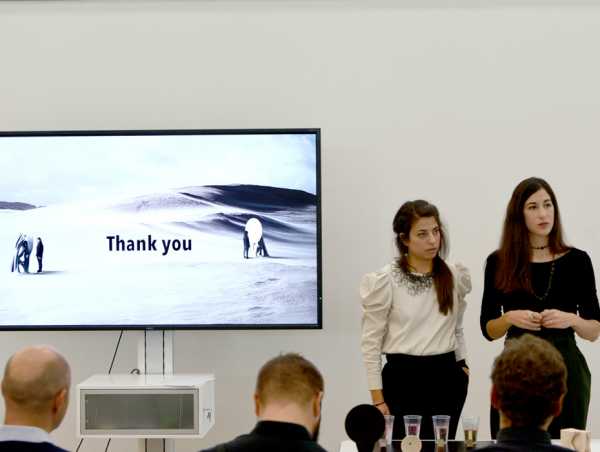
L'installation "Miroirs acoustiques" démontre le potentiel de la combinaison de la conception numérique et de l'impression 3D grand format pour l'architecture. La forme performative des miroirs est con?ue de manière ciblée pour produire un effet acoustique spatial, tout en étant optimisée sur le plan structurel afin d'utiliser les matériaux de manière particulièrement efficace.
Ce projet multidisciplinaire entre la physique et l'architecture se compose de deux miroirs concaves monolithiques de 2 mètres de diamètre. Les miroirs sont con?us de telle sorte qu'ils permettent à deux personnes de converser à voix basse sur une grande distance. Ils exploitent un effet physique que l'on retrouve dans l'architecture historique des galeries de chuchotement.
Le design organique et ornemental des miroirs a été généré par un logiciel de conception développé en interne, intégrant des paramètres acoustiques, structurels et de fabrication. Un rapport optimal entre le poids et la résistance a pu être obtenu gr?ce à la répartition ciblée du matériau le long du flux de force.
Gr?ce à l'impression 3D, les formes complexes qui en résultent peuvent être matérialisées dans un processus de fabrication entièrement automatisé et efficace en termes de ressources, avec une précision d'une fraction de millimètre.
Diaporama design
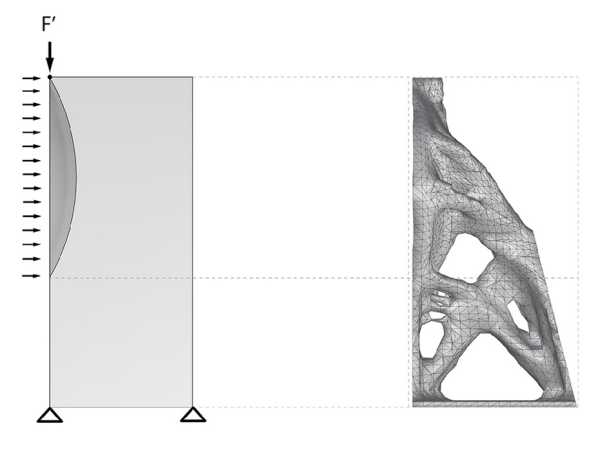
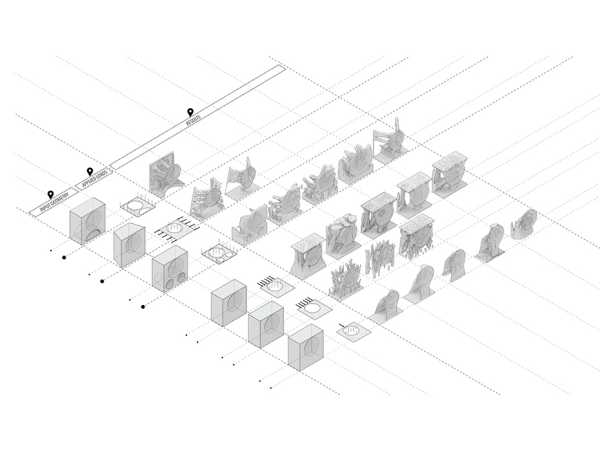
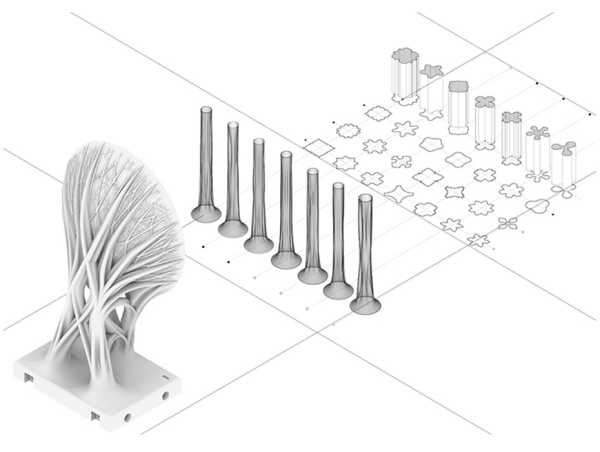
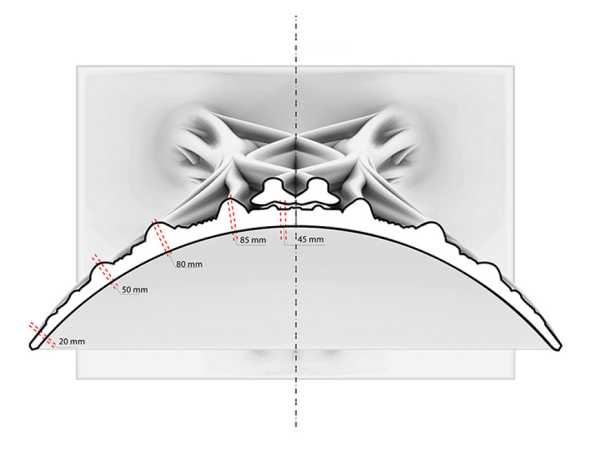
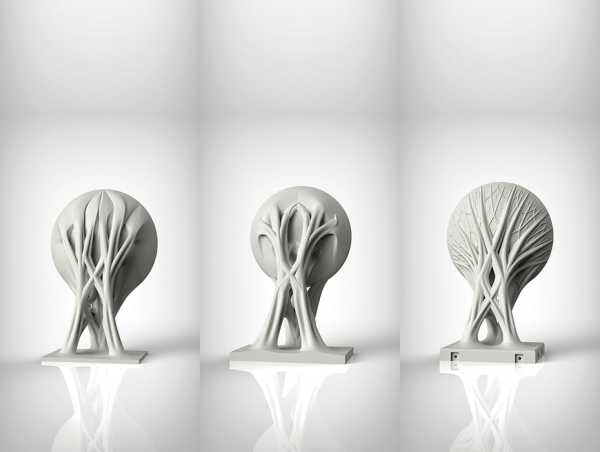
Conception assistée par ordinateur
Le projet "Acoustic Mirrors" utilise la conception assistée par ordinateur pour la recherche de formes. Le logiciel développé en interne intègre des interfaces avec un programme d'optimisation structurelle, ainsi qu'avec un logiciel de simulation acoustique.
Ce flux de travail permet d'étudier et d'évaluer plusieurs variantes de conception tout en intégrant différents critères de conception dans le processus.
En outre, l'outil de conception paramétrique développé pour ce projet permet de concevoir à la fois la structure globale et les nombreux petits détails dans un processus cohérent. Enfin, il permet d'exporter directement les données de fabrication.
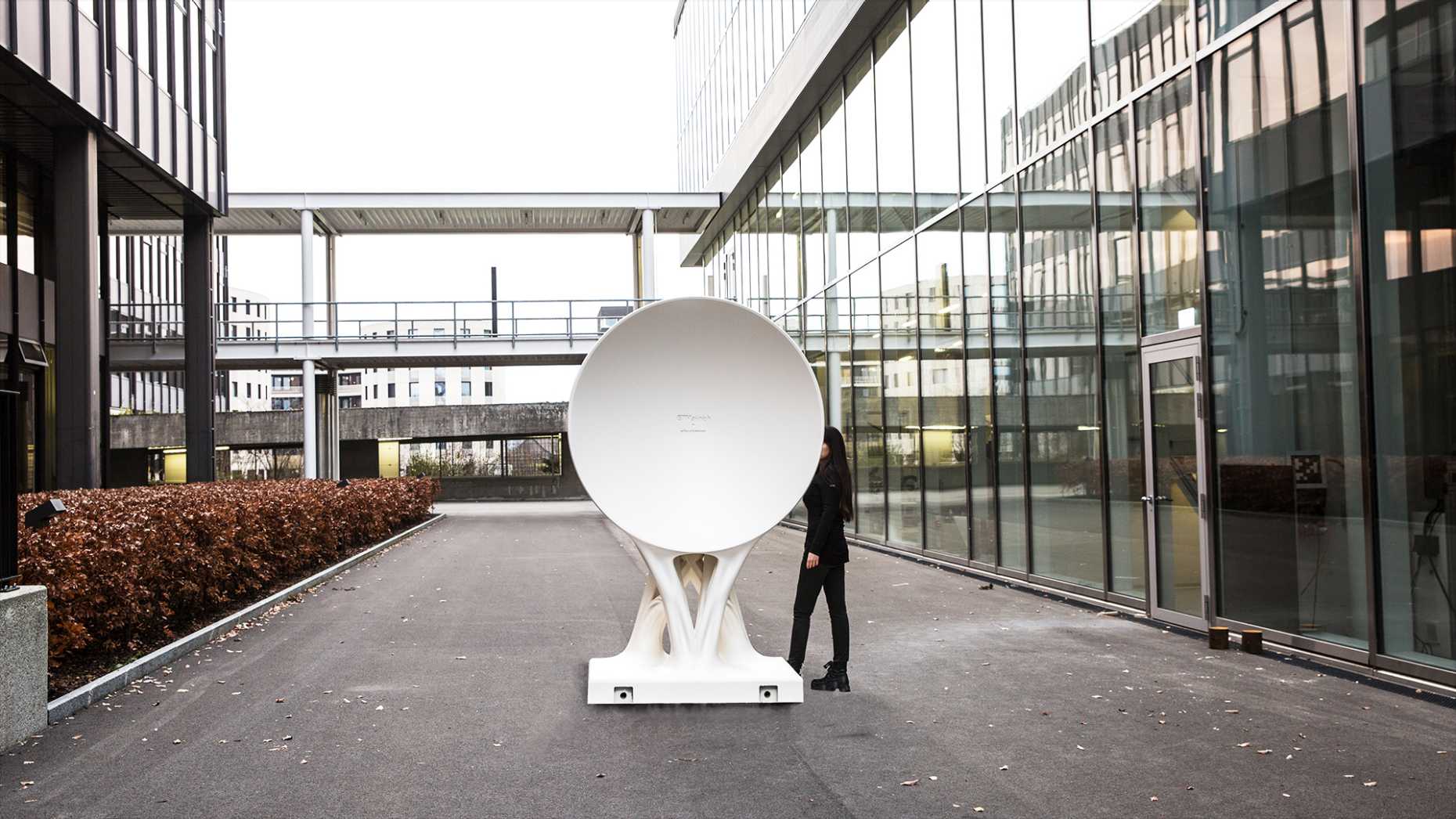
La forme générale est dominée par un segment sphérique qui réfléchit et focalise les ondes sonores. La dimension et la position de la coque sphérique sont calculées à l'aide d'un logiciel de simulation acoustique, développé par le Dr Kurt Heutschi au Signal and Information Processing Laboratory de l'ETH (ISI).
Le logiciel simule la propagation des ondes sonores réfléchies et évalue leur amplification sonore du c?té du récepteur.
L'un des objectifs de conception était l'optimisation géométrique de la structure de support qui soutient la coque sphérique, dans le but de réduire le poids total des objets.
Il fallait tenir compte des propriétés matérielles du grès imprimé en 3D - avec des propriétés similaires à celles du grès naturel, le matériau est plus résistant à la compression qu'à la flexion ou à la traction. La structure a été optimisée de deux manières : La topologie de la structure de soutien et la topographie (structure nervurée) de la coque elle-même.
Optimisation de la topologie
La structure de soutien, qui se réfère à l'architecture gothique en pierre, est optimisée pour une réduction de 30 pour cent des matériaux, tout en minimisant la déformation contre les forces verticales et horizontales (par exemple, la gravité et la pression du vent).
L'optimisation topologique appliquée trouve une répartition optimale du matériau et une disposition topologique des structures de soutien. La géométrie qui en résulte est ensuite interprétée et traduite en une forme finale.
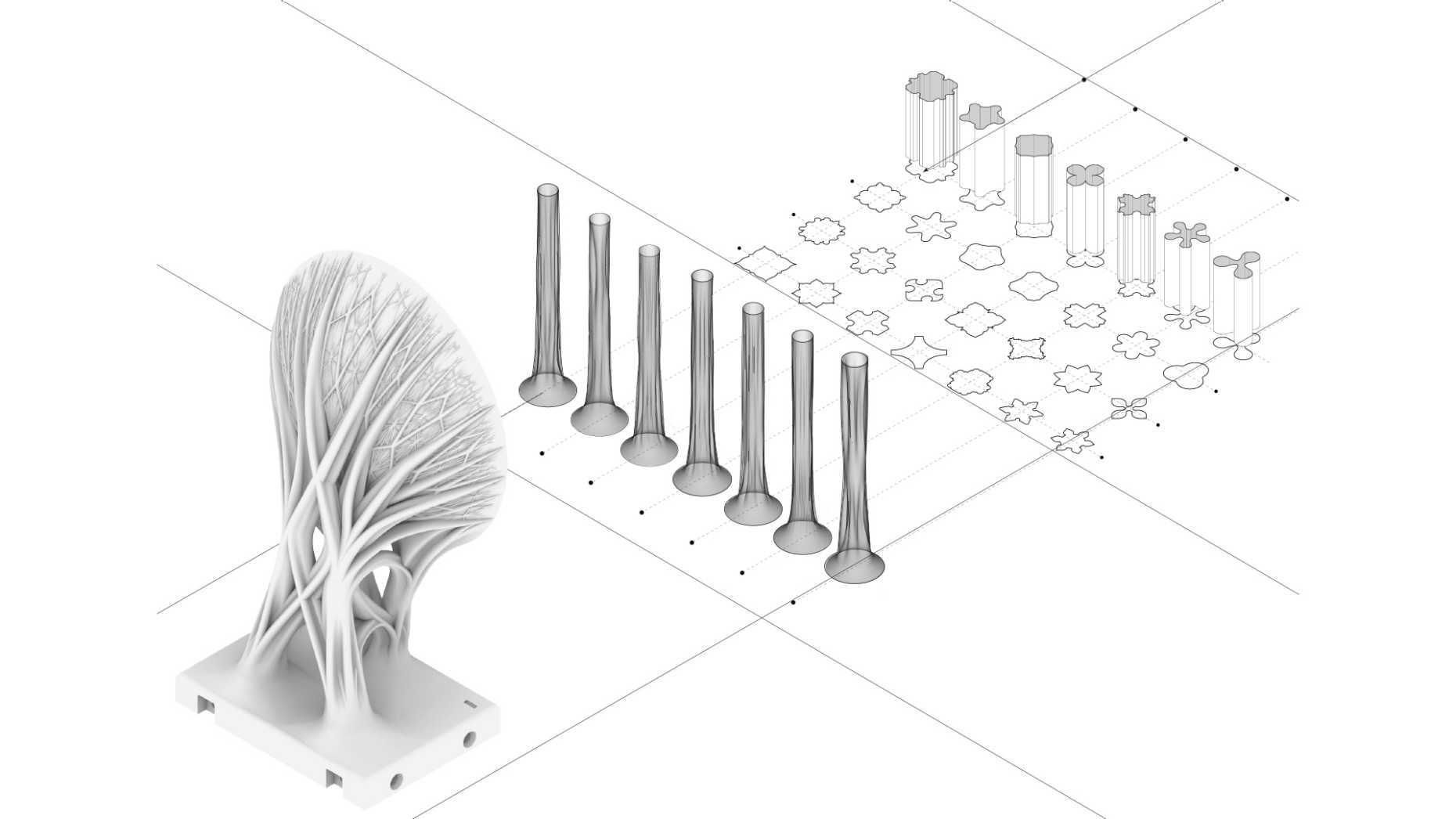
Optimisation de la topographie
La grande forme sphérique contribue pour une part importante à la masse de la structure globale. Afin de réduire cette masse et de rigidifier la coque, une microstructure organique a été con?ue en dérivation des éléments de soutien principaux, ornant toute la face arrière de nervures de rigidification. Cette optimisation de la forme/topographie a permis de réduire l'épaisseur de la calotte sphérique d'un diamètre de 1,6 mètre de 50 à 23 mm.
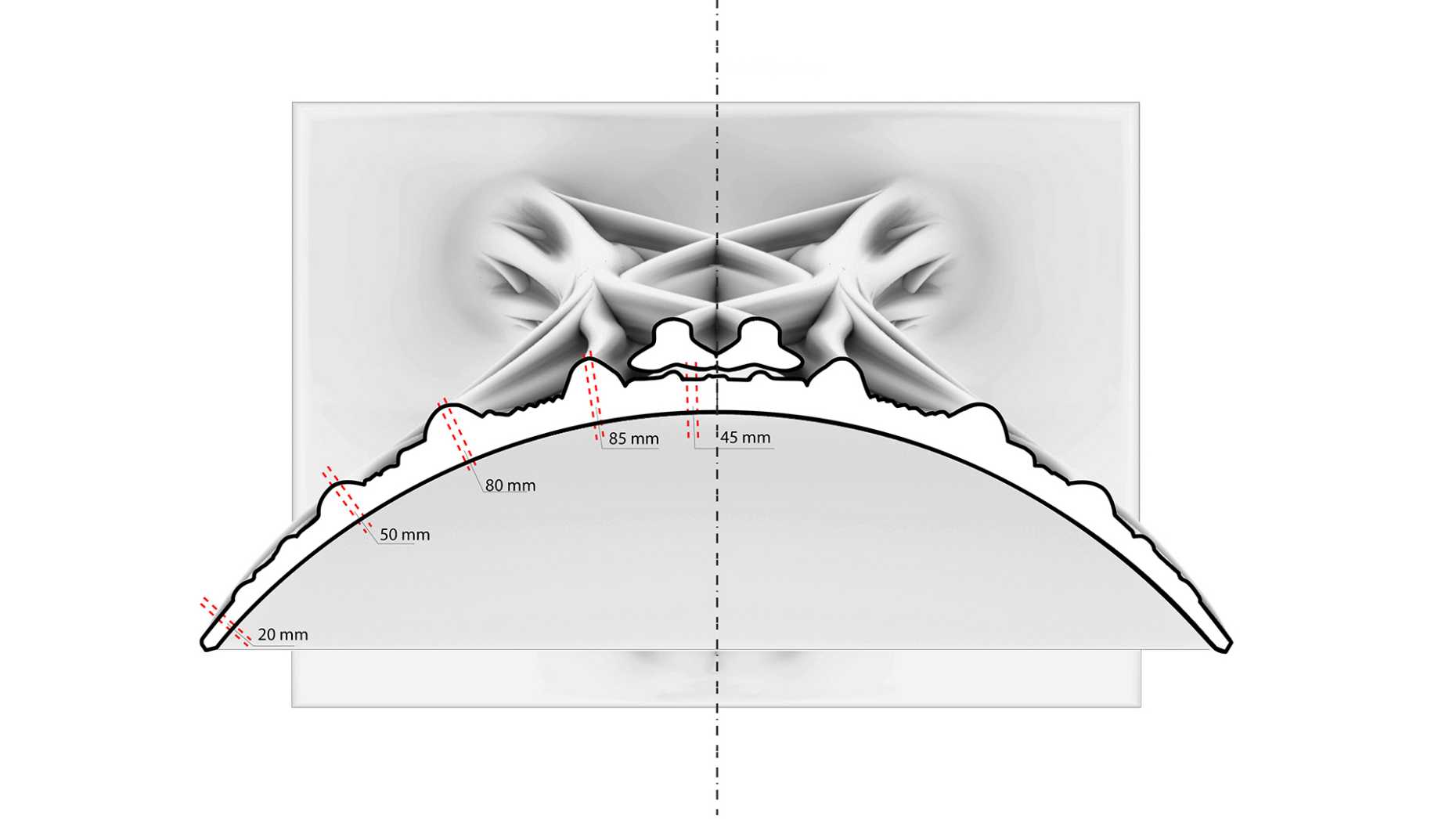
? l'instar de l'ornementation gothique en pierre, les profils des branches hiérarchiques sont modulés le long des structures et leur orientation et leur diamètre sont adaptés en fonction du cas de charge. Les nervures de la pierre sont lisses et continuellement entrelacées. Ces structures filigranes apparaissent à différentes échelles, de 100 mm d'épaisseur jusqu'à 5 mm, à chaque fois jusqu'à la limite structurelle du matériau pierreux imprimé en 3D.
Tous les détails pour le levage, le transport et le montage ont pu être intégrés directement dans le modèle 3D, de sorte qu'aucun traitement supplémentaire n'est nécessaire après l'impression 3D. Comme les miroirs ont été imprimés horizontalement en 3D, des structures de levage ont été intégrées pour permettre la rotation des structures de 600 kg. Le design a été adapté de manière à placer le centre de gravité des miroirs dans une position optimale pour le transport et le montage. Les connexions avec le sol ont été intégrées. Le foyer acoustique est indiqué à l'intérieur de la coque et des repères sont insérés sur la base pour un alignement précis sur le site.
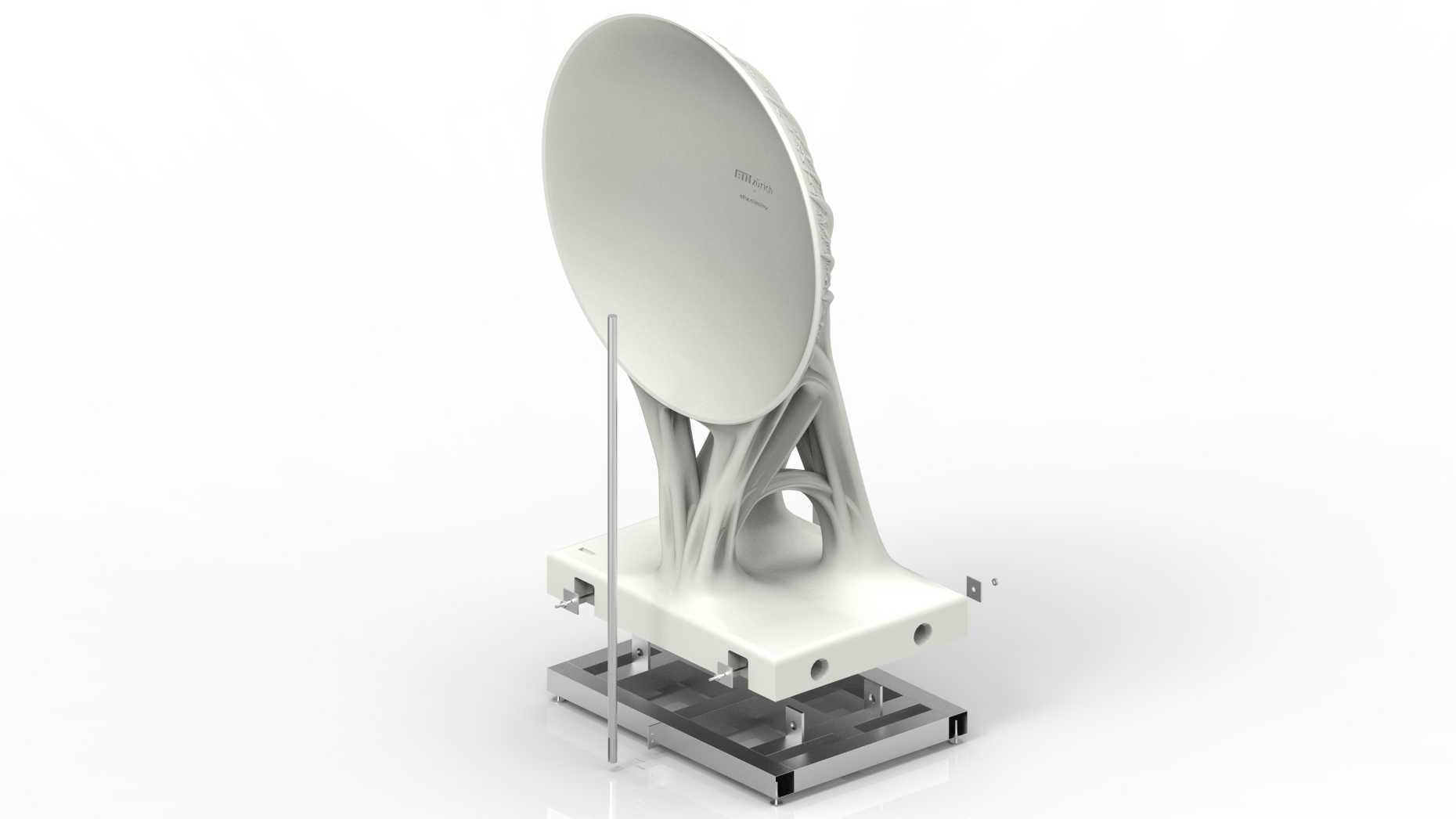
Les données de fabrication peuvent être exportées directement depuis le logiciel de conception, sans qu'il soit nécessaire de créer des plans 2D ou un modèle de fabrication supplémentaire.
Les géométries complexes des miroirs ont été fusionnées en une seule géométrie fermée, qui a ensuite été découpée en plus de 2700 couches et envoyée à l'imprimante.
Fabrication numérique par impression 3D - Fabrication additive dans l'architecture
Pour la première fois, une installation de grand format en grès artificiel pour l'extérieur a été réalisée à l'aide du procédé de jetting de liant 3D. Les deux miroirs font partie des plus grands objets fabriqués jusqu'à présent avec le procédé de Binder-Jetting. Par rapport à la fabrication des objets par coulage de béton, la fabrication additive directe présente des avantages décisifs.
- Fabrication sans coffrage : Le processus ne nécessite aucun coffrage, ce qui permet de réduire les comités et les co?ts du processus de fabrication.
- Efficacité des matériaux : Il n'est pas nécessaire de découper les matériaux et ceux-ci ne sont utilisés que là où ils sont nécessaires. Les matériaux inutilisés peuvent être recyclés à partir du processus d'impression.
- Fabrication sur mesure : L'utilisation de l'impression 3D dans le domaine de la construction promet de produire des éléments personnalisés sans générer de co?ts supplémentaires.
- Géométrie complexe : L'impression 3D permet de réaliser efficacement des géométries complexes qui, autrement, nécessiteraient plusieurs étapes de fabrication gourmandes en temps et en main-d'?uvre, ou qui ne seraient pas du tout réalisables autrement.
Binderjet 3D Printing
L'impression 3D Binderjet suit un processus qui est répété couche par couche au fur et à mesure que la hauteur augmente. Dans la première étape, du sable en vrac est réparti uniformément sur l'ensemble du lit d'impression. La deuxième étape consiste à appliquer un motif 2D de liant qui lie sélectivement le sable aux couches sous-jacentes. Aux endroits où aucun liant n'est imprimé, le sable reste en vrac. Comparée aux différentes méthodes d'impression 3D, l'impression 3D Binderjet présente des avantages spécifiques pour le secteur de la construction :
- Haute résolution : Les détails peuvent être imprimés avec une résolution d'une fraction de millimètre.
- Grandes dimensions : Un grand lit d'impression allant jusqu'à 4 x 2 x 1 m
- La plus grande liberté géométrique :Il est possible de fabriquer des formes avec des porte-à-faux et des cavités car le sable en vrac sert de support pendant le processus d'impression.
- Vitesse d'impression rapide : Gr?ce à l'utilisation de têtes d'impression industrielles, le temps de fabrication est indépendant de la complexité de la géométrie.
- Faible co?t :Le co?t des matériaux est nettement inférieur à celui d'autres procédés d'impression 3D haute résolution.
Chacun des deux miroirs acoustiques a pu être imprimé en moins de 48 heures à l'aide de la plus grande imprimante 3D industrielle Binderjet, avec un lit d'impression de 4 x 2 x 1 m pour une hauteur de couche de 0,3 mm.
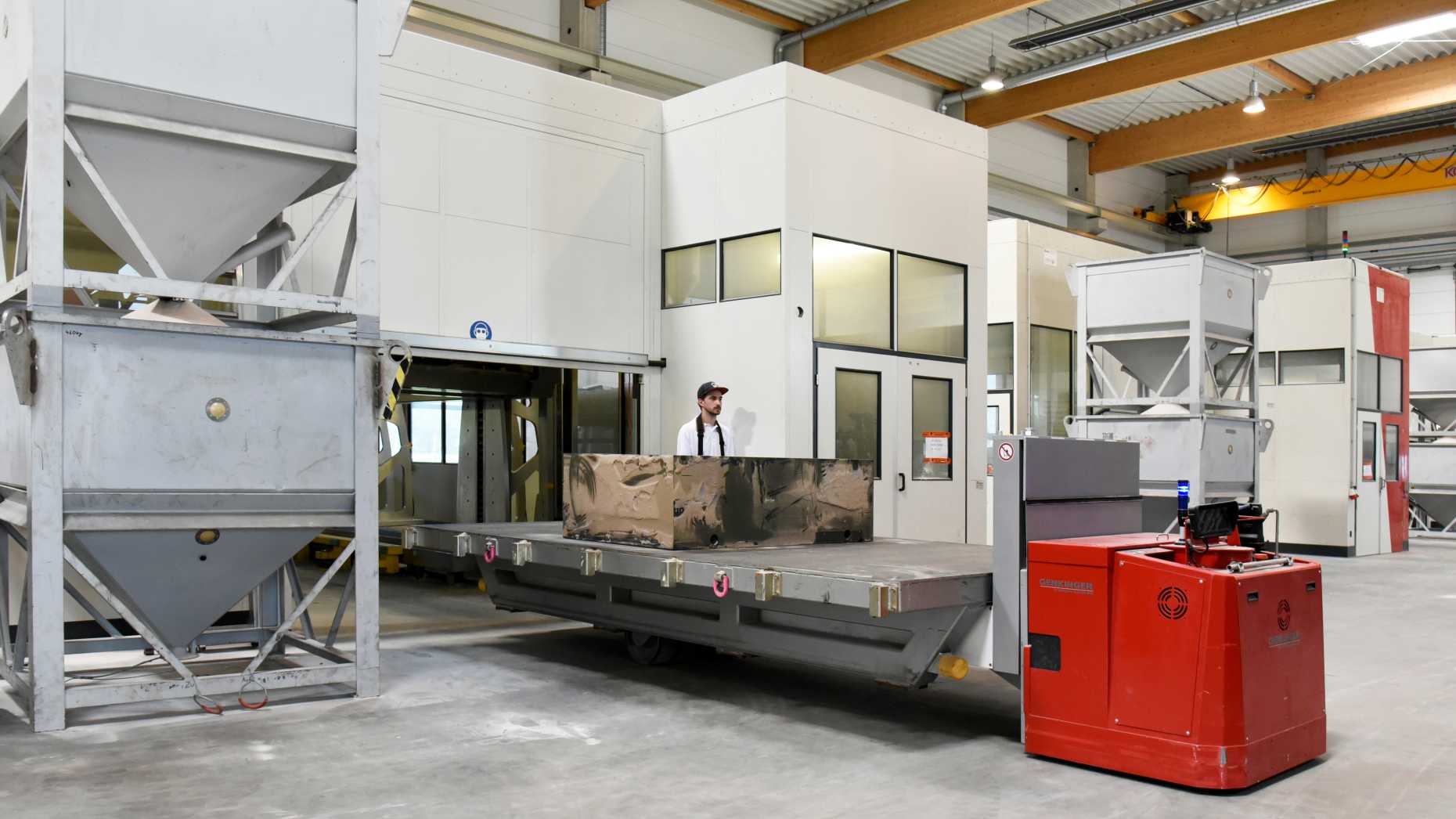
Revêtement fonctionnel
La surface du grès imprimé en 3D étant poreuse et fragile, plusieurs stratégies de revêtement ont été évaluées pour l'application en extérieur. Le scellement par pulvérisation choisi, une fine couche de résine polyester, protège la structure contre les intempéries. De plus, des tests de charge ont montré que les éléments imprimés en 3D étaient nettement renforcés par le matériau composite obtenu. Pour finir, les objets re?oivent une couche de peinture claire. Celle-ci révèle tous les détails et ornements de l'installation et garantit ainsi un contraste élevé et un jeu d'ombres à la lumière du soleil.
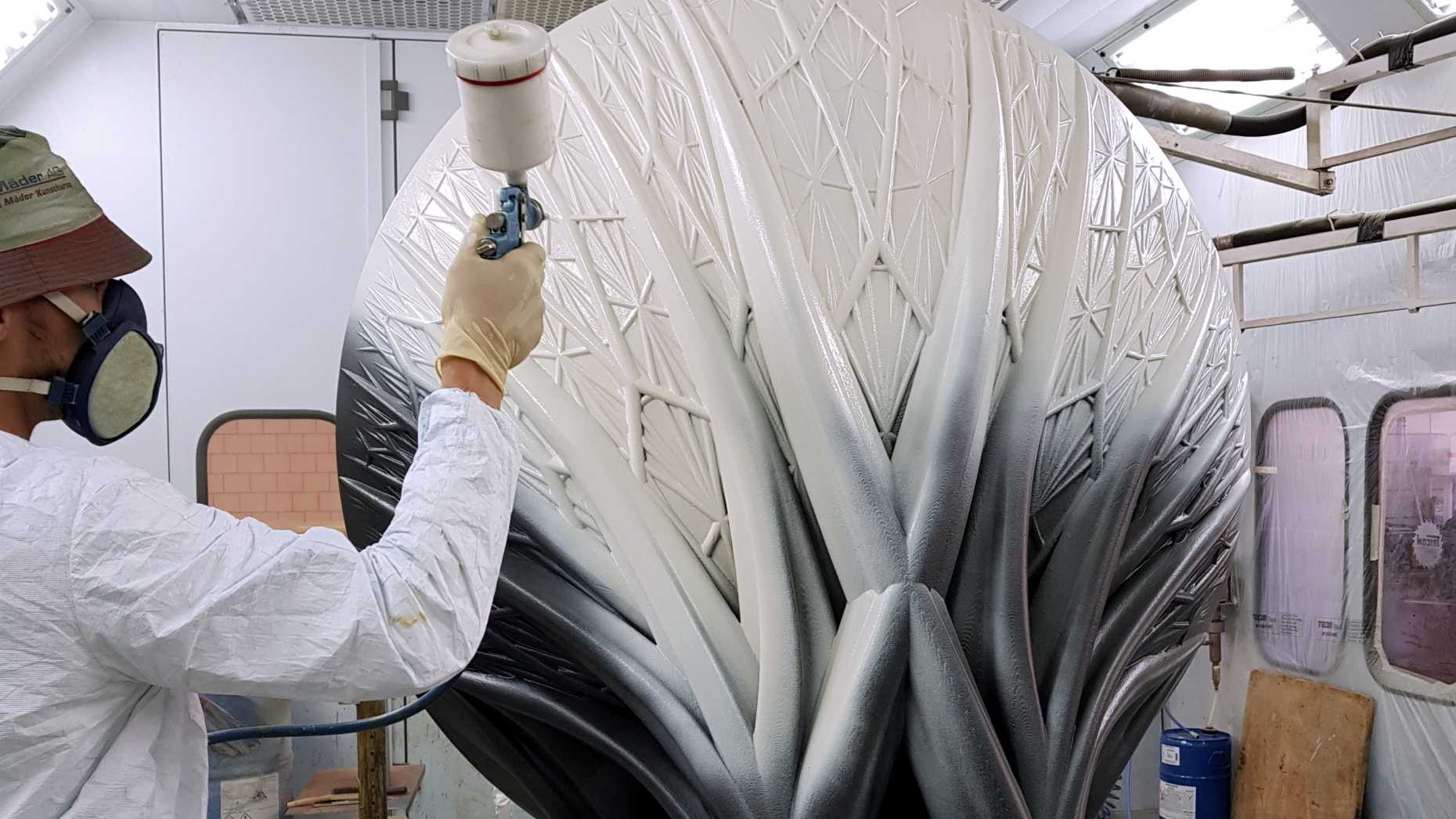
Plus d'informations sur l'équipe des miroirs acoustiques se trouvent dans le Mentions légales.
Les miroirs acoustiques en chiffres
Temps de conception : 12 semaines
Temps de fabrication : 2 jours d'impression, par miroir.
Dimensions :2.2 x 1.2 x 0.8 m
poids :600 kg
Volume : 300 litres de sable sous pression
Fichier de fabrication :plus de 5,5 millions de triangles
Granulométrie de la poudre de sable : 0.14 mm
?paisseur de couche (résolution dans la direction Z) : 0.3 mm
Résolution d'impression (résolution dans le sens X-Y) : 300 dpi